
Recently I had the pleasure of attending a seminar entitled “Trace it Back – A Course in Transparency”. Presented by Mike Johnson, 3Form’s Director of Sustainability, the course offered an engaging and practical overview of Environmental Product Declarations (EPDs), Health Product Declarations (HPDs), and the importance of these documents in the new LEED v4 rating system scheduled to go into effect this fall.
Under the LEED 2009 rating system, points can be earned by specifying rapidly renewable materials, or products manufactured with recycled content. Sourcing regional materials (those manufactured within a 500 mile radius of the jobsite) is another way to earn points. With LEED v4, the focus shifts towards a Life Cycle Analysis (LCA) and an examination of the entire manufacturing process of the product. Points are now earned for Building Product Disclosure and Optimization, and it is here that an understanding of EPDs and HPDs required for these credits becomes necessary.
To help us easily grasp the complex nature of these documents and the LCA, Mike used the analogy of an apple pie. With LEED 2009, architects and designers are mainly concerned with the final product – a baked apple pie in a tin. While we may ask questions as to the origin of the pie (regional materials) or ingredients used (recycled content), there is generally no further investigation. The LCA process will require greater transparency from the manufacturer, ultimately giving the architect and client more information. With a “cradle to gate” approach, we will know where the apples were sourced from, whether any pesticides or fertilizers were used in their production, what it takes to process the apples, what is contributed or diverted from the waste stream, the energy used in different steps of the process, and the total embodied energy of the baked apple pie in your hands. A building material LCA may even include a “cradle to cradle” approach that addresses how the product is reclaimed and reused at the end of its life.
Thus, an EPD is an executive summary from the product manufacturer of the LCA. In an effort to reduce “greenwashing” and similar unsubstantiated claims, these reports contain data that is third-party verified by a nationally recognized agency, such as UL or NSF. Each EPD is created based on the appropriate Product Category Rules (PCR) for a material, and these are governed by ISO standards. So when comparing two materials with EPDs from two different manufacturers, an architect can be sure he or she is comparing apples to apples!
An HPD is a standard report that discloses all ingredients and any known hazardous products. However, it is crucial to understand that an HPD does not document a pathway to exposure, nor does it provide an analysis of the potential risks of a product. Mike mentioned 3Form polycarbonate panels, the chemical composition of which requires Bisphenol A (BPA). In products such as polycarbonate bottles and drink ware, there is a pathway to exposure to BPA and possible health hazard from repeated and regular use. However, a panel hung on the exterior of a building made of the same polycarbonate does not provide the same pathway to exposure and therefore does not present the same risk.
Currently, manufacturer participation in EPDs and HPDs is completely voluntary. It is up to discerning architects and savvy clients to compare available products and demand greater transparency when it is found to be lacking. As manufacturers study their materials and processes there will be opportunities for optimization, with the end goal being greater energy efficiency, increasingly sustainable products, and healthier buildings.
Doug Margaretta, AIA, LEED AP BD+C
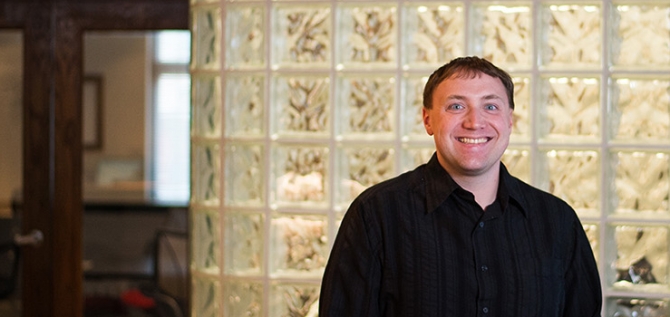